Arc welding is a type of welding that uses a welding power supply to create an electric arc between an electrode and the base material to melt the metals at the welding point. They can use either direct (DC) or alternating (AC) current, and consumable or non-consumable electrodes. The welding region is usually protected by some type of shielding gas, vapor, and/or slag.
We at Al Zahra provide Various Types of Arc Wielding procedures that are Shielded metal arc welding, Gas metal arc welding, Flux-cored arc welding, and Submerged arc welding.
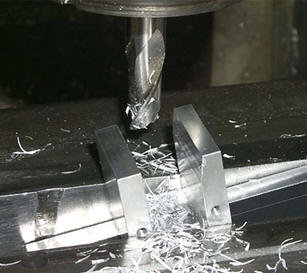
Drilling
Drilling involves the creation of holes that are right circular cylinders.
The characteristics of drilling that set it apart from other powered metal cutting operations are:
- The chips must exit out of the hole created by the cutting.
- Chip exit can cause problems when chips are large and/or continuous.
- The drill can wander upon entrance and for deep holes.
- For deep holes in large work pieces, coolant may need to be delivered through the drill shaft to the cutting front.
- Of the powered metal cutting processes, drilling on a drill press is the most likely to be performed by someone who is not a machinist.
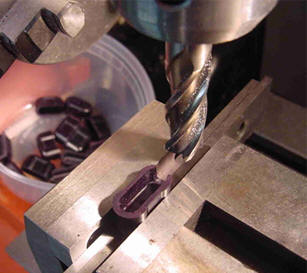
Milling
Milling is the most common form of machining, a material removal process, which can create a variety of features on a part by cutting away the unwanted material. The milling process requires a milling machine, workpiece, fixture, and cutter. The workpiece is a piece of pre-shaped material that is secured to the fixture, which itself is attached to a platform inside the milling machine. The cutter is a cutting tool with sharp teeth that is also secured in the milling machine and rotates at high speeds. By feeding the workpiece into the rotating cutter, material is cut away from this workpiece in the form of small chips to create the desired shape.
Milling is typically used to produce parts that are not axially symmetric and have many features, such as holes, slots, pockets, and even three dimensional surface contours.
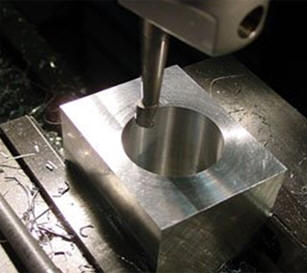
Boring
Boring is the process of enlarging a hole that has already been drilled (or cast), by means of a single-point cutting tool (or of a boring head containing several such tools), for example as in boring a gun barrel or an engine cylinder. Boring is used to achieve greater accuracy of the diameter of a hole, and can be used to cut a tapered hole. Boring can be viewed as the internal-diameter counterpart to turning, which cuts external diameters.
There are various types of boring. The boring bar may be supported on both ends (which only works if the existing hole is a through hole), or it may be supported at one end (which works for both through holes and blind holes). Lineboring (line boring, line-boring) implies the former. Backboring (back boring, back-boring) is the process of reaching through an existing hole and then boring on the “back” side of the workpiece (relative to the machine headstock).